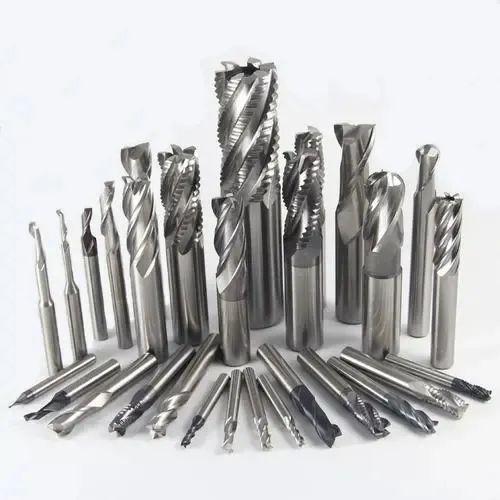
Moderni materijali za rezne alate iskusili su više od 100 godina istorije razvoja od ugljeničnog alatnog čelika do brzoreznog alatnog čelika,cementirani karbid, keramički alatisupertvrdi materijali za alat.U drugoj polovini 18. stoljeća izvorni materijal alata bio je uglavnom ugljični alatni čelik.Zato što se u to vrijeme koristio kao najtvrđi materijal koji se mogao strojno obrađivati u reznim alatima.Međutim, zbog svoje vrlo niske temperature otporne na toplinu (ispod 200°C), karbonski alatni čelici imaju nedostatak što su odmah i potpuno tupi zbog topline rezanja pri rezanju pri velikim brzinama, a opseg rezanja je ograničen.Stoga se radujemo alatnim materijalima koji se mogu rezati velikom brzinom.Materijal koji se pojavljuje da odražava ovo očekivanje je brzorezni čelik.
Brzorezni čelik, poznat i kao prednji čelik, razvili su američki naučnici 1898. Ne radi se o tome da sadrži manje ugljika od ugljeničnog alatnog čelika, već da je dodat volfram.Zbog uloge tvrdog volfram karbida, njegova tvrdoća se ne smanjuje u uvjetima visoke temperature, a budući da se može rezati brzinom koja je mnogo veća od brzine rezanja ugljičnog alatnog čelika, naziva se brzoreznim čelikom.Od 1900~-1920, pojavio se brzorezni čelik sa vanadijem i kobaltom, čija je otpornost na toplinu povećana na 500~600 °C.Brzina rezanja čelika dostiže 30~40m/min, što se povećava za skoro 6 puta.Od tada, serijalizacijom njegovih sastavnih elemenata, formirani su brzorezni čelici od volframa i molibdena.Do sada je u širokoj upotrebi.Pojava brzoreznog čelika izazvala je a
revoluciju u obradi rezanja, značajno poboljšavajući produktivnost rezanja metala i zahtijevajući potpunu promjenu strukture alatne mašine kako bi se prilagodila zahtjevima performansi rezanja ovog novog materijala alata.Pojava i dalji razvoj novih alatnih mašina, zauzvrat, doveo je do razvoja kvalitetnijih alatnih materijala, a alati su stimulisani i razvijani.U uvjetima nove tehnologije proizvodnje, alati od brzoreznog čelika također imaju problem ograničavanja trajnosti alata zbog topline rezanja pri rezanju velikom brzinom.Kada brzina rezanja dostigne 700 °C, brzorezni čelik
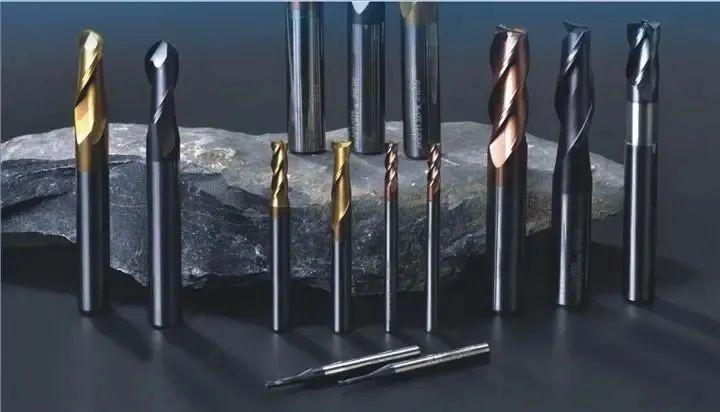
vrh je potpuno tup, a pri brzini rezanja iznad ove vrijednosti potpuno je nemoguće rezati.Kao rezultat toga, pojavili su se karbidni materijali alata koji održavaju dovoljnu tvrdoću pod višim temperaturnim uvjetima rezanja od gore navedenih i mogu se rezati na višim temperaturama rezanja.
Meki materijali se mogu rezati tvrdim materijalima, a da bi se sekli tvrdi materijali potrebno je koristiti materijale koji su tvrđi od njega.Najčvršća supstanca na Zemlji u ovom trenutku je dijamant.Iako su prirodni dijamanti odavno otkriveni u prirodi, i imaju dugu istoriju upotrebe kao alata za rezanje, sintetički dijamanti su također uspješno sintetizirani još početkom 50-ih godina 20. stoljeća, ali prava upotreba dijamanata za široku proizvodnjumaterijali za industrijski rezni alatje i dalje pitanje poslednjih decenija.
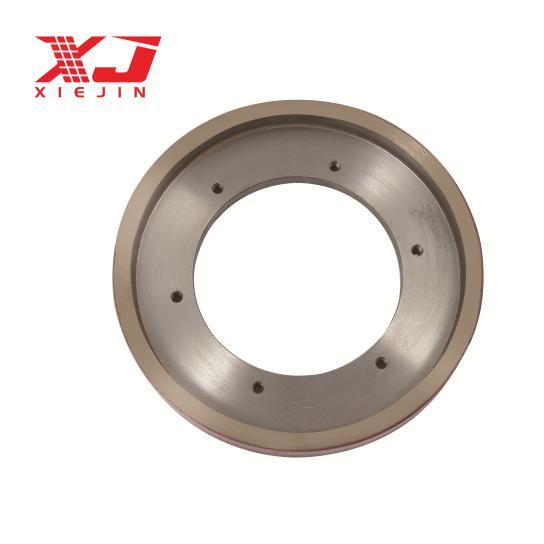
S jedne strane, razvojem savremene svemirske i vazduhoplovne tehnologije, upotreba savremenih inženjerskih materijala postaje sve obilnija, iako su poboljšani brzorezni čelik, cementirani karbid inovi keramički materijali za alatu rezanju tradicionalnih obradnih komada, brzina rezanja i produktivnost rezanja su se udvostručili ili čak desetine puta povećali, ali kada se koriste za obradu gore navedenih materijala, trajnost alata i efikasnost rezanja je i dalje vrlo niska, a kvaliteta rezanja otežana kako bi se zajamčila, ponekad čak i nesposobna za obradu, potreba za korištenjem oštrijih i otpornijih na habanje materijala alata.
S druge strane, brzim razvojem moderneproizvodnja mašinai prerađivačka industrija, široka primjena automatskih alatnih strojeva, obradni centri s kompjuterskom numeričkom kontrolom (CNC) i radionice za obradu bez posade, kako bi se dodatno poboljšala točnost obrade, smanjilo vrijeme izmjene alata i poboljšala efikasnost obrade, sve su hitniji zahtjevi. napravljen da ima izdržljivije i stabilnije materijale za alat.U ovom slučaju, dijamantski alati su se brzo razvijali, a istovremeno i razvojmaterijali za dijamantske alatetakođe je u velikoj meri promovisan.
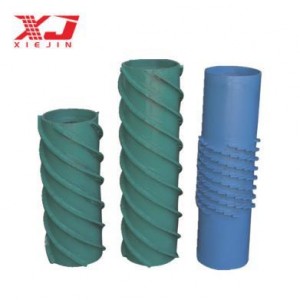
Materijali za dijamantski alatimaju niz odličnih svojstava, sa visokom preciznošću obrade, velikom brzinom rezanja i dugim vijekom trajanja.Na primjer, upotreba Compax (polikristalni dijamantski kompozitni lim) alata može osigurati obradu desetina hiljada dijelova klipnih prstenova od silicijum-aluminijske legure i njihovi vrhovi alata su u osnovi nepromijenjeni;Aluminijumske letvice za obradu aviona sa Compax glodalima velikog prečnika mogu postići brzinu rezanja do 3660m/min;Oni su neuporedivi sa karbidnim alatima.
Ne samo to, upotrebamaterijali za dijamantske alatetakođer može proširiti polje obrade i promijeniti tradicionalnu tehnologiju obrade.U prošlosti, obrada ogledala mogla je koristiti samo proces brušenja i poliranja, ali sada ne samo prirodni monokristalni dijamantski alati, već se u nekim slučajevima mogu koristiti i PDC super-tvrdi kompozitni alati za super-precizno blisko rezanje, kako bi se postiglo tokarenje. umjesto mljevenja.Uz primjenu odsuper-tvrdi alati, pojavili su se neki novi koncepti u oblasti obrade, kao što je upotreba PDC alata, ograničavajuća brzina okretanja više nije alat već alatna mašina, a kada brzina okretanja pređe određenu brzinu, radni komad i alat ne toplota.Implikacije ovih revolucionarnih koncepata su duboke i nude neograničene izglede za modernu mašinsku industriju.
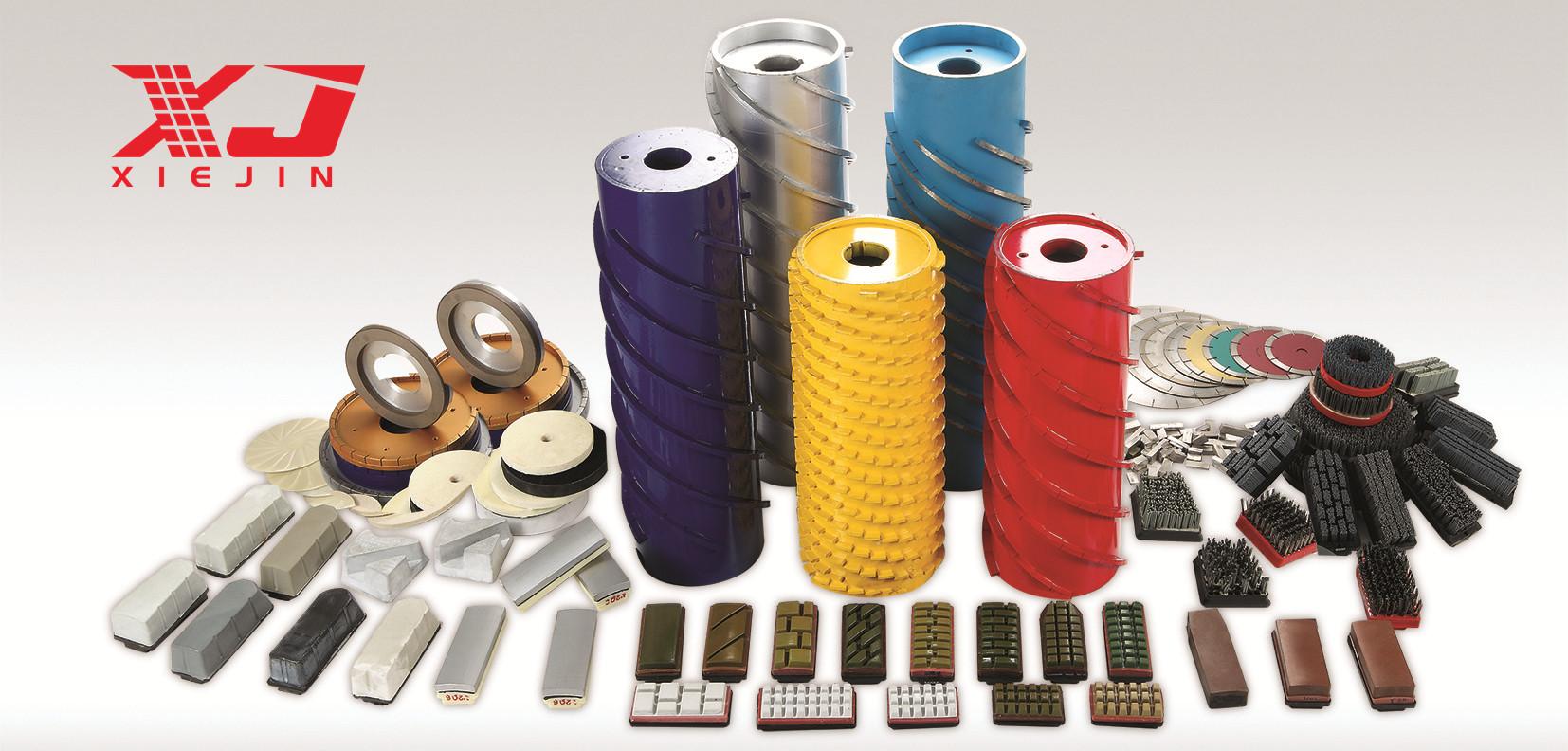
Vrijeme objave: Nov-02-2022